Nanochemistry:
Nanotubes
Synthesis
A number of techniques have been developed to produce nanotubes in sizable quantities, and advances in catalyis and continuous growth are constantly making CNTs more commercially viable. Most of these processes take place in a vacuum or with process gases. CVD growth of CNTs can occur in vacuum or at atmospheric pressure.
Arc discharge
The first macroscopic production of carbon nanotubes was made in 1992 by two researchers at NEC's Fundamental Research Laboratory, through arc discharge with a current of 100A. During this process, the carbon contained in the negative electrode sublimates because of the high-discharge temperatures.
The yield for this method is up to 30% by weight and it produces both single- and multi-walled nanotubes with lengths of up to 50 micrometers with few structural defects.
Laser ablation
In laser ablation, a pulsed laser vaporizes a graphite target in a high-temperature reactor while an inert gas is bled into the chamber. Nanotubes develop on the cooler surfaces of the reactor as the vaporized carbon condenses. A water-cooled surface may be included in the system to collect the nanotubes.
This process was developed by Dr. Richard Smalley and team at Rice University, who at the time of the discovery were blasting metals with a laser to produce metal molecules. They later replaced the metals with graphite to create multi-walled carbon nanotubes. They also used a composite of graphite and metal catalyst particles (the best yield was from a cobalt and nickel mixture) to synthesize single-walled carbon nanotubes.
This method yields around 70% and produces mainly single-walled carbon nanotubes with controllable diameter determined by the reaction temperature. However, it is more expensive than either arc discharge or chemical vapor deposition.
Plasma torch
Single-walled carbon nanotubes can be synthesized by a thermal plasma method. It was invented in 2000 at INRS (Institut National de la Recherche Scientifique in Varennes, Canada), by Olivier Smiljanic. This method aims to reproduce the conditions prevailing in the arc discharge and laser ablation approaches, but with a carbon-containing gas instead of graphite vapors to supply the carbon. This makes SWNT growth more efficient as decomposing a carbon containing gas can be 10 times less energy-consuming than graphite vaporization. It is also continuous and occurs at low cost.
Another way to produce SWNT with a plasma torch is via thermal plasma induction, implemented in 2005 by groups from the University of Sherbrooke and the National Research Council of Canada. The method is similar to arc-discharge in that both use ionized gas to increase the temperature to vaporize carbon-containing substances and the necessary metal catalysts. The thermal plasma is induced by high frequency oscillating currents in a coil, and is maintained in flowing inert gas. Carbon black and metal catalyst particles are used as feedstock, and are fed into plasma before being cooled down. In this manner different single-wall carbon nanotube diameter distributions can be synthesized.
The induction thermal plasma method yields up to 2 grams of nanotube material per minute, which is higher than the arc-discharge or the laser ablation methods.
Chemical vapor deposition (CVD)
During CVD, a substrate is prepared with a layer of nickel, cobalt iron, or a combination of catalyst particles. The diameters of the nanotubes that are to be grown are related to the size of the metal particles. This can be controlled by patterned (or masked) deposition of the metal, annealing, or by plasma etching of a metal layer. The substrate is heated to approximately 700 °C. To initiate the growth of nanotubes, two gases are bled into the reactor: a process gas (such as ammonia, nitrogen or hydrogen) and a carbon-containing gas (such as acetylene, ethylene, ethanol or methane). Nanotubes grow at the sites of the metal catalyst; the carbon-containing gas is broken apart at the surface of the catalyst particle, and the carbon is transported to the edges of the particle, where it forms the nanotubes. This mechanism is still being studied.
CVD is the most widely used method for the production of carbon nanotubes. For this purpose, the metal nanoparticles are mixed with a catalyst support such as MgO or Al2O3 to increase the surface area for higher yield of the catalytic reaction of the carbon feedstock with the metal particles. If a plasma is generated by the application of a strong electric field during growth (plasma-enhanced chemical vapor deposition), then the nanotube growth will follow the direction of the electric field. By adjusting the geometry of the reactor it is possible to synthesize vertically aligned carbon nanotubes (i.e., perpendicular to the substrate).
Of the various means for nanotube synthesis, CVD shows the most promise for industrial-scale deposition, because of its price/unit ratio, and because CVD is capable of growing nanotubes directly on a desired substrate, whereas the nanotubes must be collected in the other growth techniques.
Super-growth CVD
Super-growth CVD (water-assisted chemical vapor deposition) was developed by Kenji Hata, Sumio Iijima and co-workers at AIST, Japan. In this process, the activity and lifetime of the catalyst are enhanced by addition of water into the CVD reactor. This method is essentially a variation of CVD.
The synthesis efficiency is about 100 times higher than for the laser ablation method. The time required to make SWNT forests of the height of 2.5 mm by this method was 10 minutes in 2004. Those SWNT forests can be easily separated from the catalyst, yielding clean SWNT material (purity >99.98%) without further purification.
Natural, incidental, and controlled flame environments
Fullerenes and carbon nanotubes are commonly formed in ordinary flames produced by burning methane, ethylene and benzene. They have been found in soot from both indoor and outdoor air. However, these naturally occurring varieties can be highly irregular in size and quality because the environment in which they are produced is often highly uncontrolled. Production of uniform CNTs under controlled flame environments have promise for large-scale, low-cost nanotube synthesis based on theoretical models.
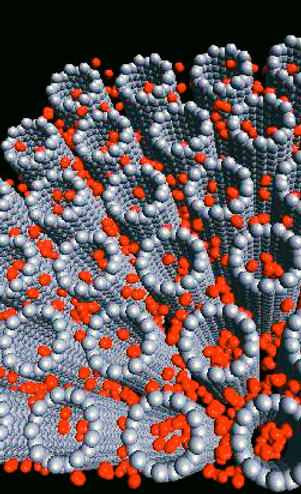